The use of organic materials is not unknown in the automotive industry. Bioplastics based on soy, sugar cane, cellulose and other organic materials can now be found in many models from all major manufacturers, be it Toyata, Lexus, KIA, Jeep, Volkswagen and more.
In 2019, automaker Ford announced that it had partnered with the University of Guelph and Competitive Green Technologies, both in Ontario, Canada, to develop a bioplastic headlight housings for the Lincoln Continental, using coffee silverskin for the first time. The silverskin comes from a McDonald's roastery while the headlight housings are molded by Varroc Lighting Systems in nearby Plymouth Michigan.
In a cooperative project between Vowalon GmbH and the Chair of Textile Technologies at Chemnitz Technical University, Volkswagen Group Innovation has now developed an artificial PVC leather whose structure consists of 51% renewable raw materials. Silverskin from the Heimbs coffee roasting plant in Braunschweig, Germany plays an important role in this.
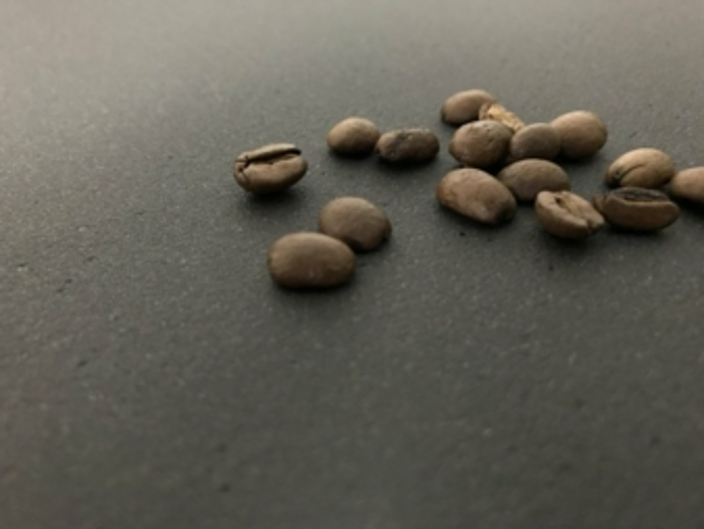
Fig. 1: During roasting of the green coffee, the protective silverskin detaches from the bean, is separated and remains as a completely dried waste material. The ground silverskin particles are then used as a filler for PVC formulations. © Volkswagen AG
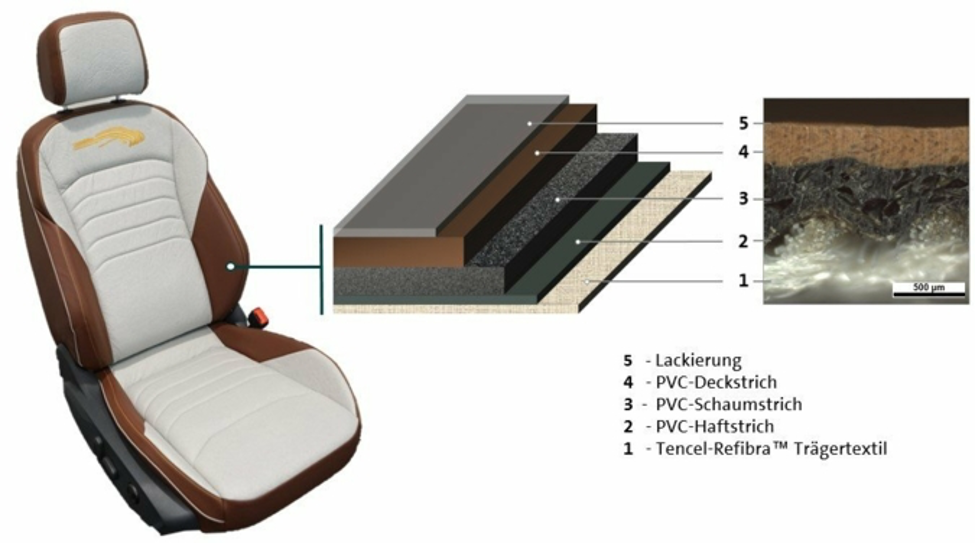
Fig. 2: The selected 3-coat structure was first implemented on a laboratory scale and then on the large-scale coating lines of Vowalon GmbH using the transfer coating process. © Volkswagen AG. Note: 5 - Varnish, 4 - top coat, 3 - foam coat, 2 - adhesive coat, 1 - Tencel-Refibra textile carrier
Among other things, finely ground silverskin, which is a waste material from coffee roasting, was used as a filler within the PVC formulation.
Studies of future vehicle concepts indicate that, driven by technologies such as autonomous driving, the vehicle interior is undergoing a transformation toward a more homelike and functionally networked interface between the vehicle and its occupants. In parallel, the desire for sustainable mobility is equally driving the development of more environmentally friendly material concepts. Due to their tangibility and direct contact, upholstery and upholstery materials within the interior of the vehicle are the focus of the occupants, as well as the automotive manufacturers and suppliers.
Since polyvinyl chloride (PVC) or polyurethane (PU) artificial leather make up a large proportion of the upholstery materials used in the interior, there is significant potential here for innovative material developments based on ecological aspects. The integration of components made from renewable raw materials within conventional and proven artificial leather structures represent a first step in the development of this potential.
In order to realize a synthetic leather structure with the highest possible proportion of renewable raw materials (and to be able to utilize established large-scale production processes, the associated process sequences and empirical values), a conventional PVC foam synthetic leather structure was selected since it can be produced by the transfer coating process.
Selection of potential fillers
In order to substitute and thus minimize the proportion of non-renewable raw materials, three elements of the overall structure were identified: PET carrier textile, synthetic plasticizer formulation and calcium carbonate filler within the PVC plastisol.
As potential fillers for PVC formulations, three agricultural waste/byproducts were considered in more detail in terms of their availability, processing and alternative uses:
- Coffee silverskin: Part of the coffee bean husk, waste from the roasting process.
- Treber/pomace: residues of the mash from beer, wine or whiskey production
- Sugar beet pulp: residue of sugar extraction.
Since spent grains and sugar beet pulp have residual nutrient content even after the brewing process or sugar extraction, they are usually used as animal feed or fermented in biogas plants and are therefore not considered waste materials but rather as byproducts. Due to a high residual moisture content, these materials would also have to undergo energy-intensive drying in order to be used as fillers in plastics.
In contrast, the coffee silver skin represents a complete waste material in coffee production. During roasting of the green coffee, this protective silverskin detaches from the bean, is separated from the bean and remains as a completely dried waste material.
Knitted from sustainable raw materials
In addition to the ground silverskin particles as a filler, a formulation made from biological raw materials was added to the PVC-Plastisole, instead of the synthetic plasticizer. The textile carrier was a knitted fabric made from Tencel-Refibra yarn, about one-third of which is produced from industrial cotton waste and used textiles and two-thirds from wood pulp using the Lyocell process.
The selected 3-coat structure was first implemented on a laboratory scale and then on the large-scale coating lines of Vowalon GmbH using the transfer coating process (see Fig. 2). The top coat forms a compact and resilient surface layer, while the foam coat ensures that the overall structure has a defined volume and flexibility through additional expansion. A bond between these two layers and the textile substrate is generated by the adhesive coating. Finally, the material is embossed with an adjustable surface structure and sealed with a coating.
Through the combination of the individual elements described above, it was possible to create a synthetic leather structure that, with a total share of 51%, consists largely of renewable raw materials. Contrary to the associated significant reduction in petrochemical components, material properties were also achieved that allow direct comparison with conventional PVC foam artificial leather.
Note:
Except the first two paragraphs, this post is a slightly modified translation of the article “Kunstleder mit Kaffeeschalenfüllstoff” ("Imitation leather with coffee silverskin as filler material"), released by Volkswagen AG; Author: Lars Lewerdomski, COI Sustainability Solutions Bio-Materials and Polymers, Volkswagen AG. Published in: Textile Network, 2021.10.29.
Postscript:
Communication with the author of the original article was extremely pleasant and straightforward. Unfortunately, it was not possible for Mr. Lewerdomski to answer questions such as the respective percentages of the three organic materials (in particular, of course, the percentage of silverskin), the amount of silverskin per car seat, whether the silverskin is processed into a bioplastic, whether the artificial leather is already being produced or when it will be produced, for which models it is intended, whether the use of the organic materials results in noticeable cost savings in production, etc. Answering all these questions would have to go through the internal approval process, which could take time. I therefore prefer to keep my eyes and ears open and wait for further publications and announcements from Volkswagen AG or Volkswagen Group Innovation.
One thing is clear, however: the "Bio Lab" at Volkswagen was founded only a few years ago. And in a feature on Germany's Zweitem Deutschen Fernsehen, Martina Gottschling, an engineer at Volkswagen Group Innovation who conducts research on innovative materials for Volkswagen, added the following to the comment that the synthetic leather is not yet biodegradable: "The synthetic coffee leather is a first step on the way [there]. We are striving ... to make a current solution more ecological. That is, we are really focusing on new materials." The commenter concludes by pointing out the decision to move into the next stage of prototype development with the synthetic coffee leather.